5 Manufacturing Industry Trends
Upgrade Your Manufacturing Process:
5 Trends That Increase Manufacturing Efficiency
The recent globalization trends increased competition between manufacturers across the globe. Consumers are now opting for manufacturing companies that could cater to their personalization requirements. Manufacturers are also enhancing cybersecurity along with the implementation of new systems. The development of various technological advancements such as AI integrations in production processes and operations are creating notable impacts in the efficiency and success of manufacturing industries.
Here are the Top 5 Manufacturing Industry Trends we can expect in 2024:
1
Industry 5.0
Although the use of robots in the manufacturing industry has been continuously increasing, industry 5.0 is more focused on the human centric approach highlighting the collaboration between humans and machines to make processes more efficient and accurate. Compared to industry 4.0, the main goal of industry 5.0 is to provide a unique and more personalized experience to consumers along with the technology by utilizing the technologies brought by industry 4.0.
We all know that human’s cognitive ability is irreplaceable, and combining it with advanced technologies will open more doors in improving processes, especially manufacturing. Since most industrial processes require decision making, incorporating human touch to technologies will drive customer satisfaction through personalization. This coexistence will benefit manufacturers by equipping capable individuals with advanced technologies that are suited for them, this also leads to providing a better service for the clients. Since industry 5.0 is more about adding human touch to technological advancements such as collaborative robots (cobots), employees must also continue to upgrade their technical skills to be able to keep up with the updated developments.
2
Digital Twin
Digital Twin technology is a virtual replica of any real-world operation. It enables manufacturers to streamline their processes by increasing visibility across operations, understand performance of an equipment, and run tests scenarios which improves planning and efficiency. Since a digital twin is an exact copy of a physical operation, it needs to store massive amounts of data. Digital twins can also be useful whenever a company is planning to implement a new system for the first time. Testing out the operability and integration can be quite expensive to test in the real world and may disrupt operation especially when something goes wrong. These tests can be carried out in the digital world without risking physical operations. Whenever you are planning to make some changes to your production but not quite sure on how it affects other systems, you can first test it out with your digital twin. Digital twins are not only convenient in experimentation, it also allows you to monitor various equipment and measure its productivity which allows you to plan ahead and fix systems before they malfunction.
Alongside with its implementation, proper security measures and data management also needs to be practiced. It is also necessary to provide know-how with the new technology, planning ahead with the interoperability, and onboarding technical experts contributes to a smooth transition. Although implementation and data management seems complex, the benefits of having a real-time, real-world, and integrated view of operations that improves process and decision making to advance your manufacturing operations.
3
Industrial Internet of Things (IIoT)
IIoT systems are equipped with distributed computing enabling users to process across multiple devices, connecting industrial machines, sensors, and other production equipment to the cloud. The sensor receives and analyzes data and forwards it to the designated system that automates workflows. Imagine your workflow having checkpoints, and all those checkpoints have sensors that record and analyze each data then forwards it to your system where you can track each process in real time. These smart sensors are also helpful in quality control. For example, a smart sensor can detect whether there is an odd element in a product by differentiating its weight, size, temperature etc. which makes quality check more precise than manual inspection.
Manufacturers can now monitor operations remotely, reduce errors, predict equipment defects in an early stage, and enhance asset traceability allowing for faster and more accurate decision making. Proper IIoT implementation improves manufacturing, supply chain, and production efficiency by allowing remote monitoring and control. IIoT systems are also equipped with encryption and authentication features to reduce vulnerability in software attacks. With machine learning algorithms and distributed computing to process data across multiple devices, IIoT enabled systems makes maintenance easier compared to traditional automated systems.
4
Smart Manufacturing
In these modern times, automated factories are considered to be more efficient and reliable. Businesses continue to grow with the demand, faster procurement and interoperability becomes a priority. Smart Manufacturing integrates all resources and processes providing you with real-time evaluation and analysis of your manufacturing operations. In contrast to traditional manufacturing which manually optimizes processes, smart manufacturing does it automatically and gives you full traceability. Equipped with advanced features such as predictive analytics and big data, it enables you to streamline processes making manufacturing as efficient as possible by identifying bottlenecks including predictive maintenance and energy optimization. Being able to manage workflows, production, inventory, and track processes using your phone or tablet adds to the convenience. Reducing time consumed in performing manual tasks and organizing data by integrating multiple systems allows you to spend time on other necessary tasks.
Smart manufacturing management technologies can also include digital twins, IIoT, AI and other modern technologies for a seamless data exchange. Since most small to medium manufacturers still use outdated software, it is better to update their software that can run modern versions of applications and can be integrated with sensors. You can start piloting a certain part of your process where you can measure the outcome of the changes in your business model from traditional to digital. If the results are proven to contribute in streamlining the manufacturing process, you can gradually implement it to other systems as well.
5
Enhanced Cybersecurity
Over the previous years, the manufacturing industry is recorded to be one of the most targeted industries in cybercrimes. According to Statista’s report, 24.8% of cyberattacks on 2022 targeted manufacturing industries. (Source: Statista)
One of the challenges that manufacturer’s face is their vulnerability to cyberattacks. Sometimes, due to outdated systems and lack of centralized systems that immediately notify suspicious activity and by the time a suspicious activity is detected, it’s already too late to prevent data breach. As new technologies and integrations emerge, the risk of cyberattacks increases and managing multiple systems against hackers becomes complex. Just like any other industries, it is also necessary for manufacturers to have countermeasures to protect their data, avoid downtime, and avoid problems caused by cybercrimes. Cyberattacks could be mitigated by implementing appropriate security measures such as: regular security check ups, using anti-virus or anti-malware, monitoring information transfers ensuring that data are only available to designated key persons and partners. Consider having recovery systems to guarantee immediate resume of operations.
Continuous practice of control, availability, integrity, confidentiality (CAIC) could avoid leakage of sensitive data. Control user access on multiple systems. Evaluate possible entry points for hackers and strengthen the security including hiring data security experts or providing training to those who are involved in security as well as teaching security measures to employees when handling company data.
In order to ensure effective results in implementing digital trends, one must understand how the system works to fully utilize its performance and features. Blindly following trends without properly analyzing what is appropriate for your business and clients would be a waste of resources. It is recommended to study the pain points that you want to address in your operations first then look into different software providers that match your goals. Implementing these changes also require a collaborative environment and continuous upskilling. Modern issues require modern solutions that can keep up with the consumer’s ever changing demands. Oftentimes, new technologies also require new technicians. Consulting with experts or hiring specialists leads to a smooth transition and can provide appropriate technical solutions and technical support. Of course, digitalization doesn’t stop there, manufacturers need to continuously update systems and policies to prevent accidents that can disrupt the operation such as cyberattacks, irregular system maintenance, and outdated practices that don’t match operation or client needs. Updates does not only refer to technical upgrades but also design such as the User Interface (UI) and User Experience (UX) of your software. Modern UI/UX designs that are properly categorized are easier to use therefore would also be easier to implement and adapt for new users. When you think of the design, you must also think about compatibility and accessibility. Nowadays, software that is compatible to operate using phone, tablet, wearables, etc. are becoming more popular. Resources that are accessible and easy to use will make employee’s performance more productive. Updating your processes to current trends will keep your business relevant to the current and upcoming demands.
Take the first step to digitization
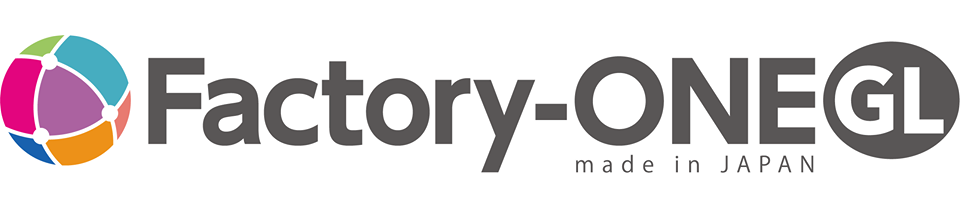
Factory-ONE GL is a manufacturing management software that offers multiple features such as Order Management and Inventory Management that can be implemented in various industries.
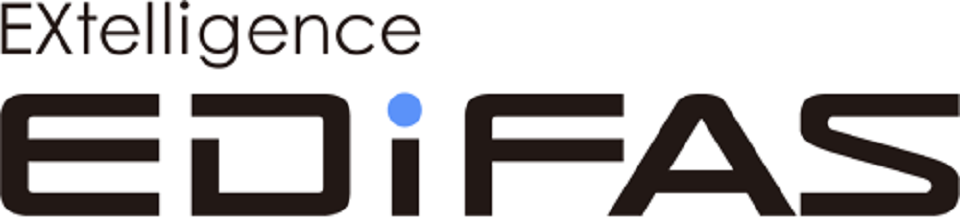
EXtelligence EDIFAS is a cloud-based EDI (Electronic Data Interchange) service that supports SCM (Supply Chain Management), B2B, IoT, and other integrations at an affordable price.