Japanese Manufacturing Techniques
Japanese Manufacturing Techniques
And Its continuous influence in modern manufacturing
Manufacturing industry contributes a lot to the economy of every nation. While the latest technologies emerge, some traditional techniques are still being implemented today. Japan has long been recognized for its innovative and efficient manufacturing techniques. These methods have set the bar high and continue to influence production worldwide. Even with the rapid advancement of technology and new manufacturing trends, many traditional Japanese techniques are still relevant today in contributing to the success of manufacturing enterprises.
5S: Workplace Organization
Have you ever walked into a workspace and immediately felt overwhelmed by the clutter? The 5S methodology aims to tackle this problem by promoting a clean, organized, and efficient workplace. The 5S stands for Sort, Set in order, Shine, Standardize, and Sustain.
Each step of the 5S process helps create an environment where tools and materials are easy to find, reducing wasted time and increasing productivity. For example, in a factory, this might mean having clearly labeled storage bins, regular cleaning schedules, and standardized workstations.
While 5S originated in Japan, it has been embraced worldwide, particularly in lean manufacturing environments. Companies that implement 5S often see immediate benefits in terms of improved workflow and morale. It’s a simple yet powerful technique that ensures the workplace supports efficiency rather than hindering it.
Kaizen: Continuous Improvement
One of the most well-known concepts: Kaizen. This philosophy is all about continuous improvement. Kaizen isn’t just a business strategy; it’s a way of life in many Japanese companies. It involves everyone from the CEO to the factory floor workers in the pursuit of constant, gradual improvements.
Kaizen encourages employees to look for small ways to improve their work processes every day. This could be anything from reorganizing tools for better efficiency to suggesting new ways to reduce waste. For example, Toyota has famously adopted Kaizen to refine its production lines, leading to higher quality cars and more efficient manufacturing processes. The principles of Kaizen have been so effective that they’ve been adopted globally, proving that this traditional Japanese method remains invaluable in modern manufacturing.
Poka-Yoke: Mistake-proofing
Imagine a world where human error in manufacturing is virtually eliminated. This is the goal of Poka-Yoke, a technique designed to prevent mistakes before they happen. The term Poka-Yoke translates to “mistake-proofing” or “fail-safe”.
Poka-Yoke can be as simple as designing a part that can only fit one way or as complex as integrating sensors that detect anomalies during production. For instance, in an assembly line, a Poka-Yoke device might be a fixture that ensures parts are correctly oriented before they are assembled. This method is crucial in maintaining quality and consistency, especially in industries where precision is paramount, like electronics and automotive manufacturing.
By incorporating Poka-Yoke, companies can reduce defects, improve safety, and save on the costs associated with rework and recalls. It’s a small change that can lead to significant improvements, embodying the spirit of Kaizen.
Just-In-Time (JIT) Production
JIT is a strategy developed by Toyota to increase efficiency and decrease waste by receiving goods only as they are needed in the production process. This means that manufacturers keep their inventory levels very low and order supplies just in time to meet demand.
JIT has been a game-changer in manufacturing because it minimizes the costs associated with excess inventory and reduces the time products spend in storage. It also forces companies to be more precise in their production planning and scheduling. Today, JIT is a standard practice in many industries beyond automotive, including electronics, apparel, and even food production. Its ability to streamline operations and improve responsiveness to market changes makes it a timeless technique.
Jidoka: Automation with a Human Touch
Jidoka, also known as “automation”, is a concept that empowers machines to detect problems and halt production automatically, allowing humans to intervene and address issues. This ensures that defects are caught immediately, rather than allowing faulty products to continue down the production line.
Jidoka began with Toyota’s founder, Sakichi Toyoda, who invented a loom that would stop automatically if a thread broke. This principle has been applied broadly across manufacturing sectors, integrating smart technology with human oversight to maintain quality control.
Today, Jidoka is especially relevant in the era of Industry 5.0, where automation and human collaboration are key. By combining intelligent machines with human expertise, manufacturers can achieve high levels of efficiency and quality, ensuring that the final product meets the standards.
Conclusion
As we move further into an era dominated by advanced technology and automation, these traditional Japanese techniques will likely continue to evolve, maintaining their core principles while adapting to new challenges. Japanese manufacturing techniques have not only stood the test of time but continue to be relevant in modern manufacturing operations. From the continuous improvement principles of Kaizen to the precision and quality control of Poka-Yoke and Jidoka, these techniques embody a commitment to excellence that resonates globally. The widespread adoption of methods like Just-In-Time production and 5S organization highlights their universal applicability and enduring relevance. These practices reflect the good reputation that Japanese manufacturers built, emphasizing on delivering product quality and customer satisfaction globally.
Take the first step to digitization
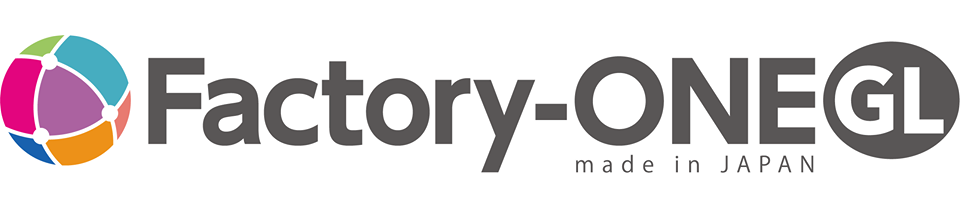
Factory-ONE GL is a manufacturing management software that offers multiple features such as Order Management and Inventory Management that can be implemented in various industries.
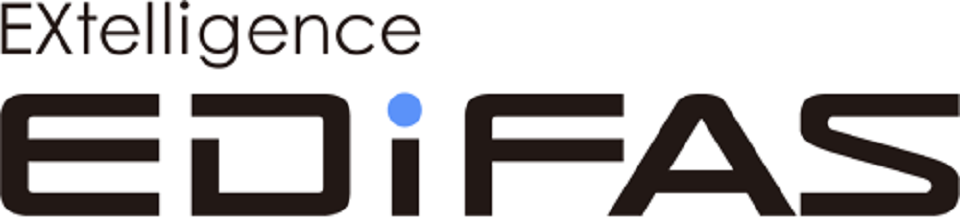
EXtelligence EDIFAS is a cloud-based EDI (Electronic Data Interchange) service that supports SCM (Supply Chain Management), B2B, IoT, and other integrations at an affordable price.